WOOD
Advanced Material Technology
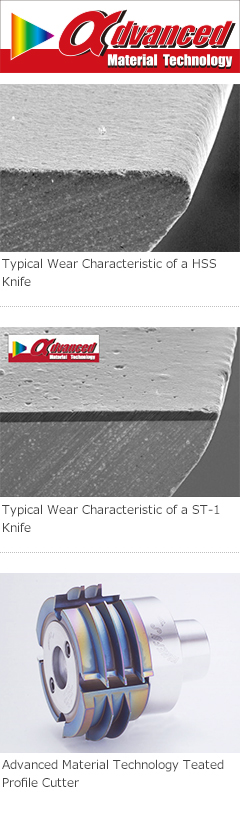
Kanefusa is the pioneer and worldwide leader in the development of advanced cutting edge materials for the wood working industry.
The first product treated with Advanced Material Technology were ST-1 planer knives, which we started selling in 1995.
Today we have two treatments for different substrate materials.
HS-HP is applied to cutting edges with a High Speed Steel substrate.
HC-UP is applied to cutting edges with a Tungsten Carbide base.
Both treatments change the wear characteristics of cutting edges. The results are extensively longer edge life and outstanding surface finishes when machining solid wood. Tools treated with advanced material technology can be re-sharpened multiple times with conventional grinding equipment.
- The User Value is
-
- 3-15 times longer edge life depending on the application leads to a better machine utilization for more output and less grinding cost due to less regrinds per year
- Smooth and tear-out free cut surface
- Reduction of manufacturing costs due to higher process stability and significant lower rejection rates due to torn grain and other defects
- Due to less residue adhesion, permanent higher feed speed can be realized
- Tools run quieter and power consumption does not increase significantly during run time
PCD - Fusion Technology
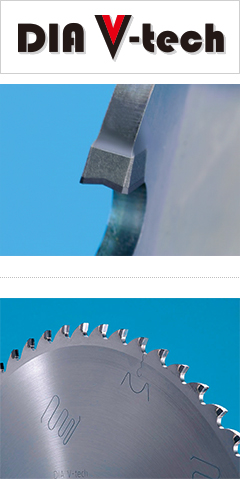
Polycrystalline Diamond (PCD) is considerably harder and wear resistant than tungsten carbide enabling tremendous longer tool life. However, due to the brittleness of the PCD, the cutting edge geometry of a PCD sawblades is less aggressive compared to a that of a Tungsten Carbide Tipped sawblade. In result, the cut quality is inferior to that of a T.C.T. sawblade.
We have developed a V-shaped rake side tooth geometry for PCD tipped sawblades, which cuts aggressive like a T.C.T. sawblade. In result the tool life is 30 to 40 times longer and the sawblades cuts tear out free laminated particleboard or MDF.
In order to manufacture such a tooth shape, it was necessary to invent a technology that allows fusing single PCD elements together. After years of research, we have successfully developed this technology. The first product available with two single pieces of PCD fused into a V-shaped tip is the V-tech PCD sawblade.
V-tech sawblades are very suitable for use on vertical panel saws and table saws to cut plastic or paper laminated MDF and particleboard.
- The User Value is
-
- Longer edge life than a T.C.T. sawblade and an excellent cut finish allows tremendous cost savings in the manufacturing process
- DIA V-tech sawblades can be re-sharpened several
- Runs very straight because the cutting forces are in balance